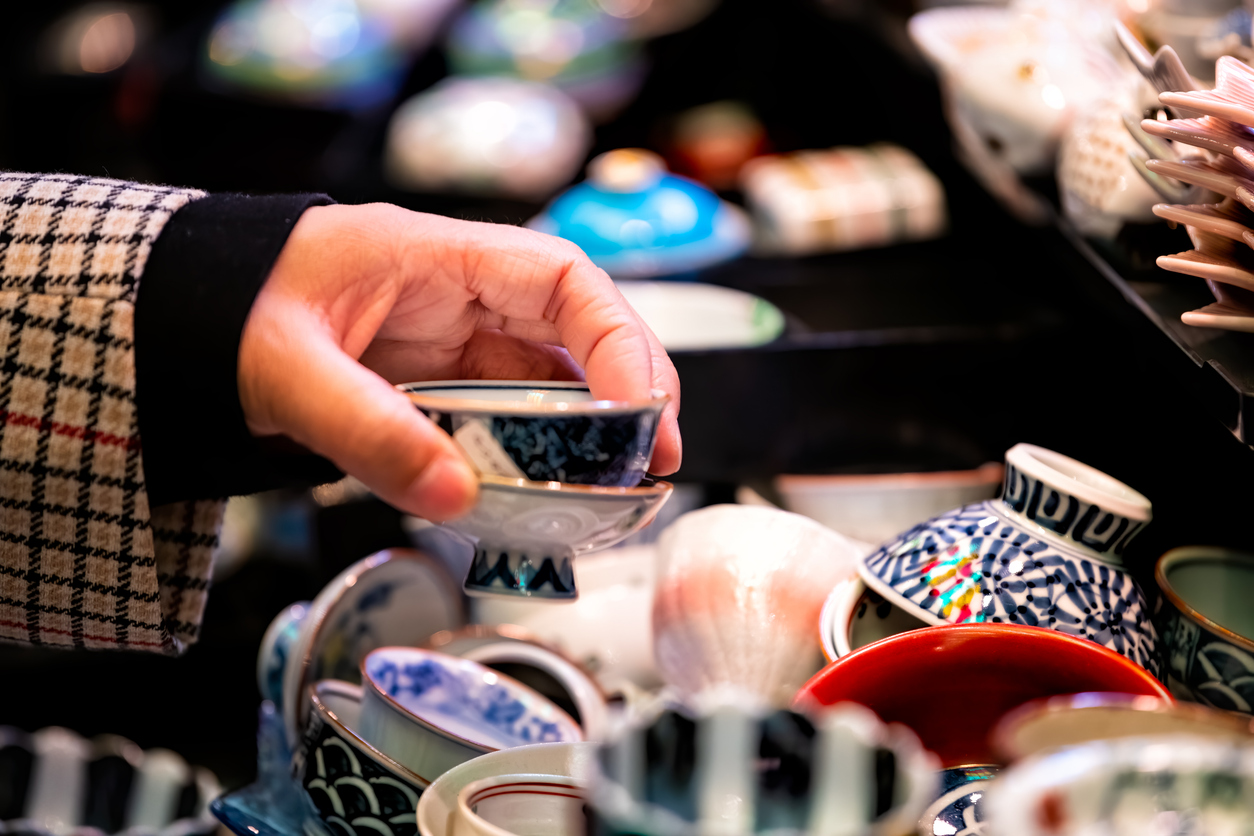
業種 | 漆器のEC販売 |
販売形態 | BtoC |
導入前の課題
ー在庫の置き場所の把握が難しい
熟練者しか在庫の保管場所が分からないため、作業が属人化していた。
ピッキングの際に時間がかかり、間違いも頻発していた。
ー無駄な行動が多い
作業動線が非効率で、ピッキングミスが多発していた(週に7~10件発生)。
出荷作業が定時(18時)に終わらず、最終集荷時間(18時40分)までに間に合わなかった。
集荷時間に間に合わないため、スタッフが片道30分かけてベースセンターに荷物を持ち込む必要があった。
定時後の残業が常態化しており、20時まで作業が続いていた。
ー固定ロケーション管理の課題
在庫管理が固定ロケーション方式だったため、決められた場所にしか商品を保管できなかった。
商品の数量が増えると、スペースの確保が難しく、管理が煩雑になっていた。
導入効果
ーピッキングミスの削減
毎日1件以上発生していたミスが大幅に減少し、ミス0件の日が増えた。
ー作業の効率化
ピッキングの最適化により、作業がスムーズになった。
18時40分の集荷時間までに作業が完了し、荷物の持ち込みが不要になった。
残業が削減され、セール時期でも定時(18時)に作業が終わるようになった。
ー出荷対応力の向上
以前は出荷件数が1,000件を超えると作業が困難だったが、現在は最大1,500件まで対応可能。
出荷件数が増えても余裕を持って作業できるようになった。
ー在庫管理の柔軟性向上
固定ロケーションから柔軟な管理方式へ変更し、スペースの有効活用が可能になった。
商品の数量が増えても適切に管理できるようになった。